Redefining architecture with industrialised construction
Industrialised construction is revolutionising the world of architecture, offering efficient, sustainable and high quality solutions. Although it faces logistical and perceptual challenges, the advantages it offers in terms of time, cost and flexibility position it as a viable and attractive alternative for the future of construction.
Differences between prefabricated, modular and industrialised construction
Traditionally, homes are built doing all the work directly on the site, but in recent years systems have been developed that allow part of the construction work to be performed in a workshop or factory.
The terms modular, prefabricated and industrialised construction are used to describe different approaches and techniques. Each has specific features, advantages and applications:
- Prefabricated construction consists of manufacturing construction elements (such as walls, ceilings and floors) in a controlled factory. These components are then transported to the site to be assembled. Prefabrication allows for high quality control and reduces on-site work, minimizing delays and optimizing the use of materials. This method is ideal for projects that require speed and efficiency, such as industrial buildings and office buildings.
- Modular construction involves the creation of complete modules in a factory, including the proportional part of installations and all their interior finishes. These modules are transported to the site where they are assembled as blocks. The modular construction stands out for its speed and flexibility in design, being a popular choice for hotels, residential complexes and educational structures.
- Industrialised construction takes prefabrication one step further by utilising industrial production methods and advanced technologies such as robotics and CNC machines. This approach standardises processes, improves accuracy and reduces waste. The elements are manufactured in a factory and assembled on site quickly and efficiently. Industrialised construction is ideal for large-scale projects that require a high level of precision and quality control.
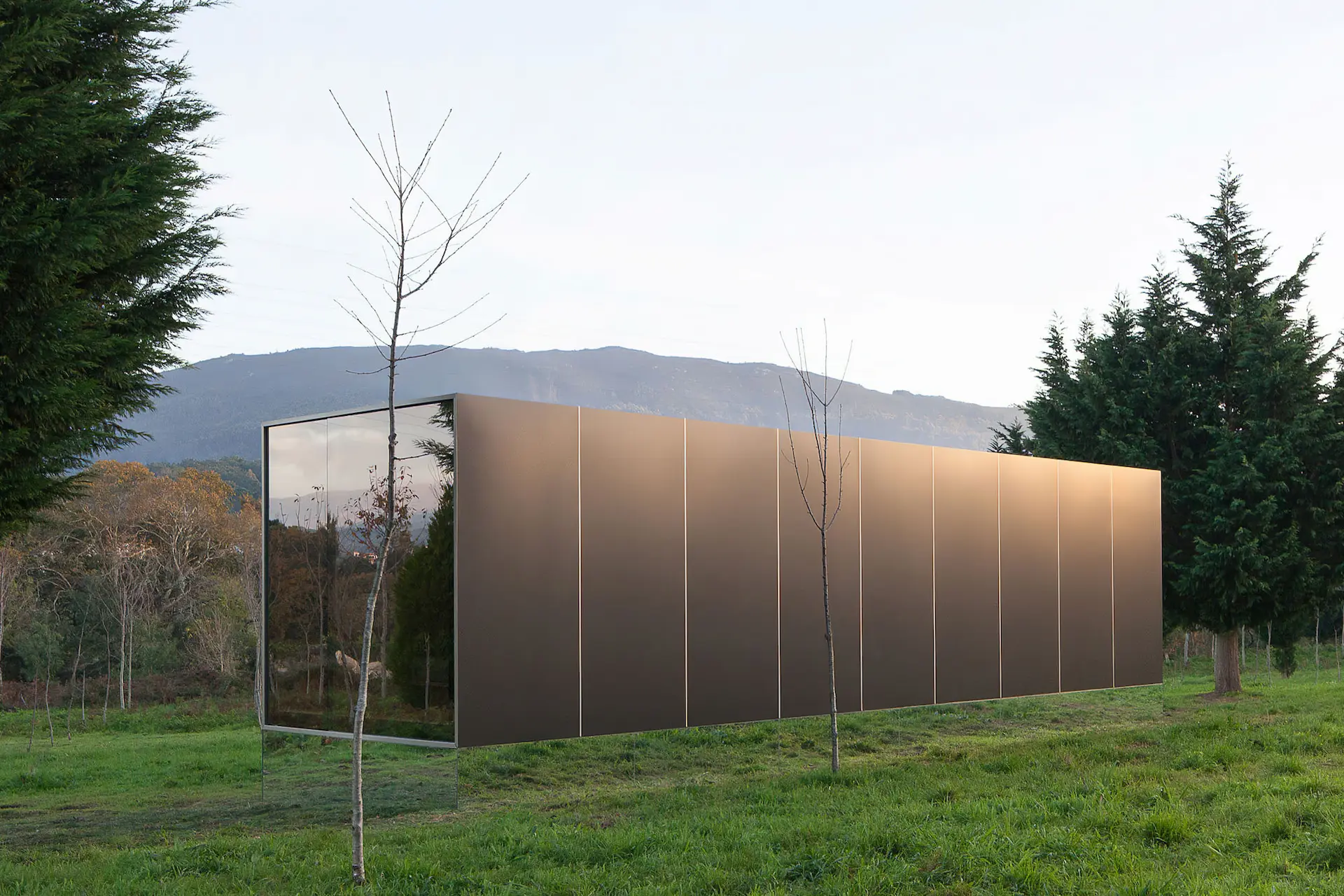
Advantages of industrialised construction
industrialised construction offers multiple benefits that make it an attractive option for modern architectural projects:
- Efficiency in times and costs: The simultaneous production of components in the factory and their assembly “in situ” allows significantly reduced construction times. This minimises delays and costs associated with prolonged works.
- Quality and Accuracy: When manufactured in controlled environments, components undergo rigorous quality inspections, reducing common errors in traditional constructions and improving accuracy. This constant control ensures that each piece meets the highest standards before being shipped to the site
- Sustainability: The materials and processes used in industrialised construction are usually greener than traditional methods. Efficiency in the use of materials and the reduction of waste contribute to a lower environmental footprint. In addition, modular buildings can be designed to be disassembled and reused.
- Flexibility and Adaptability: Modular buildings can be designed to be expanded, reconfigured or even moved as needed. This offers versatile solutions that adapt to different requirements and enable future changes without the need for expensive demolitions.
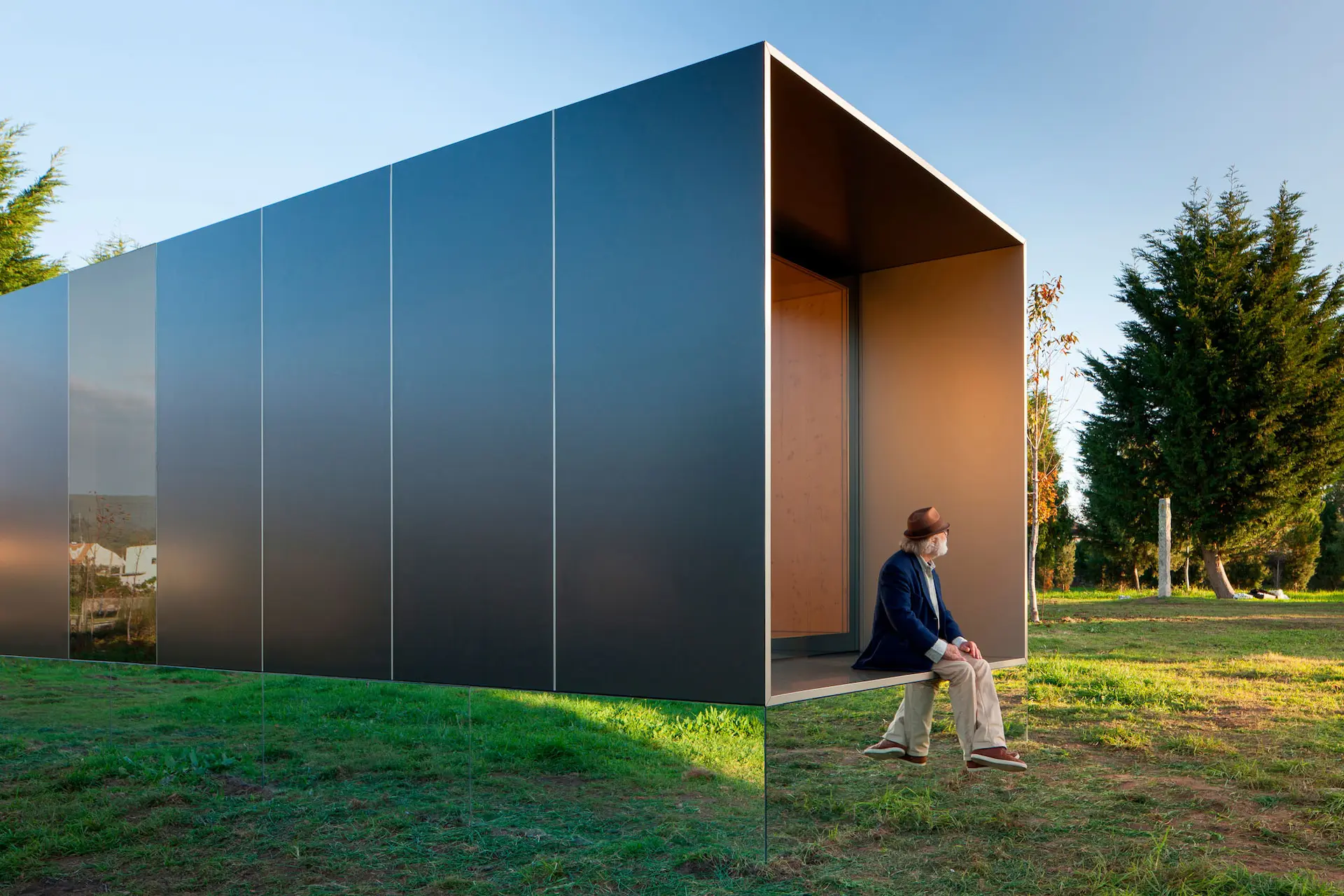
Challenges of industrialised construction
Despite its numerous advantages, industrialised construction faces several challenges:
- Logistics and Transportation: Transportation of large modules from the factory to the site can be complex and expensive, especially in remote or difficult to access areas. It is crucial to consider the distance between the factory and the site, as well as the emissions generated during transport.
- Financing: Getting funding for industrialised construction projects can be a significant challenge. Traditionally, banks release funds progressively as project stages are completed, which may not align well with the industrialised construction model, where much of the work and costs are concentrated at the start of the project on component manufacturing. This can cause cash flow problems for contractors. However, some banks are beginning to adapt, offering more flexible financing models that better match the requirements of industrialised construction.
- Market Perception: There is a perception in some markets that modular construction is less durable or aesthetically limited compared to traditional methods. Although it allows flexibility, there are limitations in terms of size and complexity of designs, especially in high-rise projects.
Outstanding examples of industrialised construction
There are notable examples worldwide that highlight the ability of industrialised construction to carry out high-rise projects without problems. Here are two of the most important projects that have generated a great impact:
- Living Building in Changsha, China: Built by the Broad Group, this 10-story modular building was assembled in just 28 hours, demonstrating the speed and efficiency of this method. This project has been widely covered and praised in specialist media for its innovative approach and speed of construction.
- AC NoMad Hotel in New York, USA: This hotel, developed by Marriott, is the tallest modular hotel in the world. Its construction was a milestone for the industry, showcasing how modular construction can literally reach new heights in terms of design and functionality. This project has received considerable media attention and has been cited as an example of how modular construction can revolutionize the construction of tall structures.