Transformation and machining processes for composite panels: We shape your ideas
The many possibilities offered by the machining and transforming processes of the aluminium composite panel allow the design of façades without creative limits.
In case you do not have the necessary equipment, our production centre can carry out the machining, punching and die cutting, stamping, edging, bending and forming operations that the project requires.
Thanks to STACBOND’s advanced technology it is possible to create 3-D shapes, reliefs and play with light on the skin of the building, to personalize the façade making it a unique work.
STACBOND’s Technical Office works closely with architects, designers and installers to bring the most avant-garde proposals to life.
Machining
of composite panels
STACBOND composite panels can be machined using CNC machinery or manually with a wall saw or portable router.
This process allows you to prepare the exact measurement and easily shape the parts to be installed on the façade, using the different certified assembly systems from STACBOND, with visible or hidden fixings, as well as to adapt the panel to a wide variety of other applications.
The STACBOND technical office has specific programs that minimize material waste during machining of parts, minimising cut-offs and waste in the process.
Preparation of cassettes to cover the façades by suspended systems. Panels with customized shapes and perforations to improve the aesthetics and functionality of the façades. Manufacture of furniture and decorative elements for interiors such as counters, shelves and partition panels with custom designs and complex details.
Industrial applications such as covers for electronic equipment, control panels and machinery structures.
Specify the exact dimensions and shapes required for the panel, including cuts, perforations and any specific design details. Specify the tolerances and accuracy required for panel machining, ensuring that it meets the structural and strength requirements of the project.
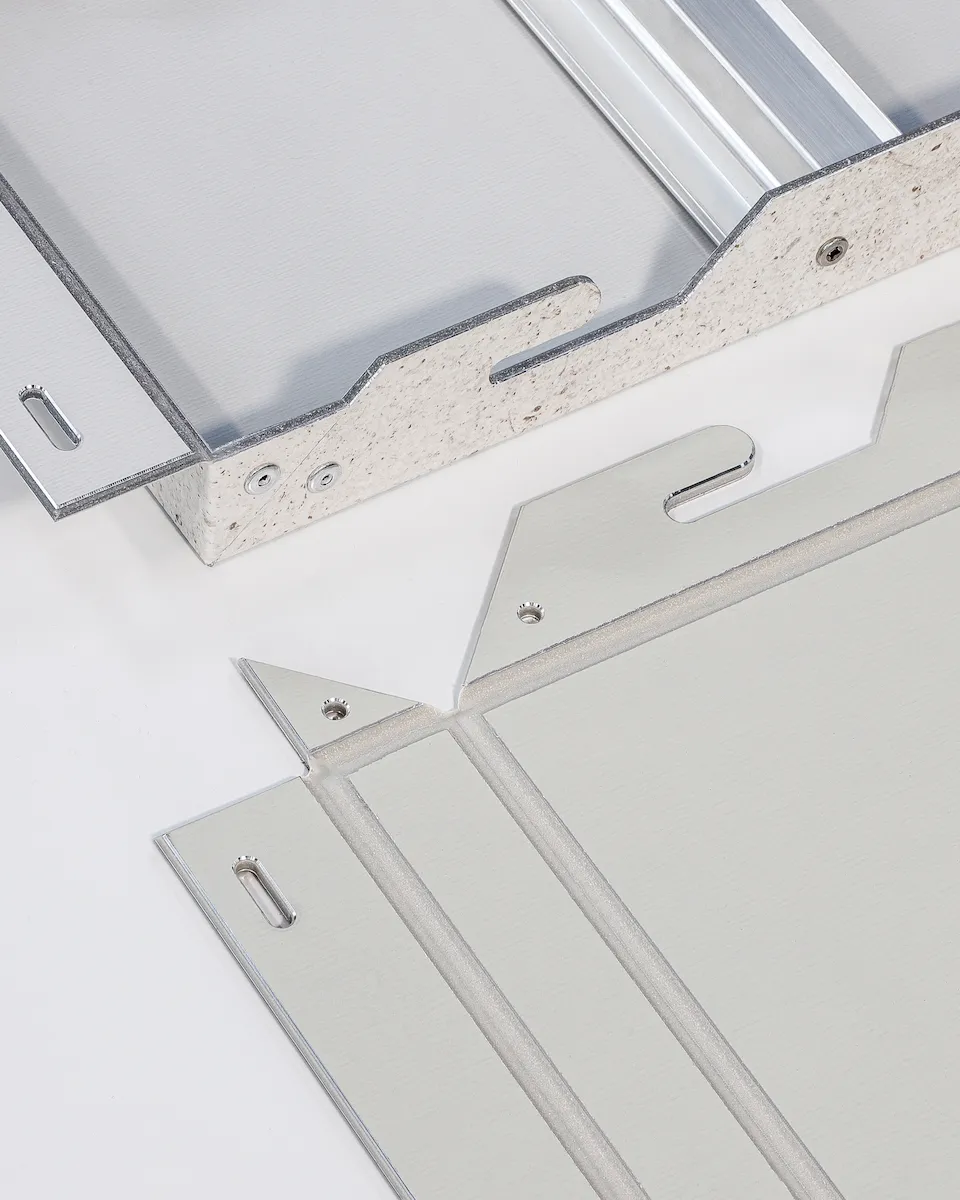
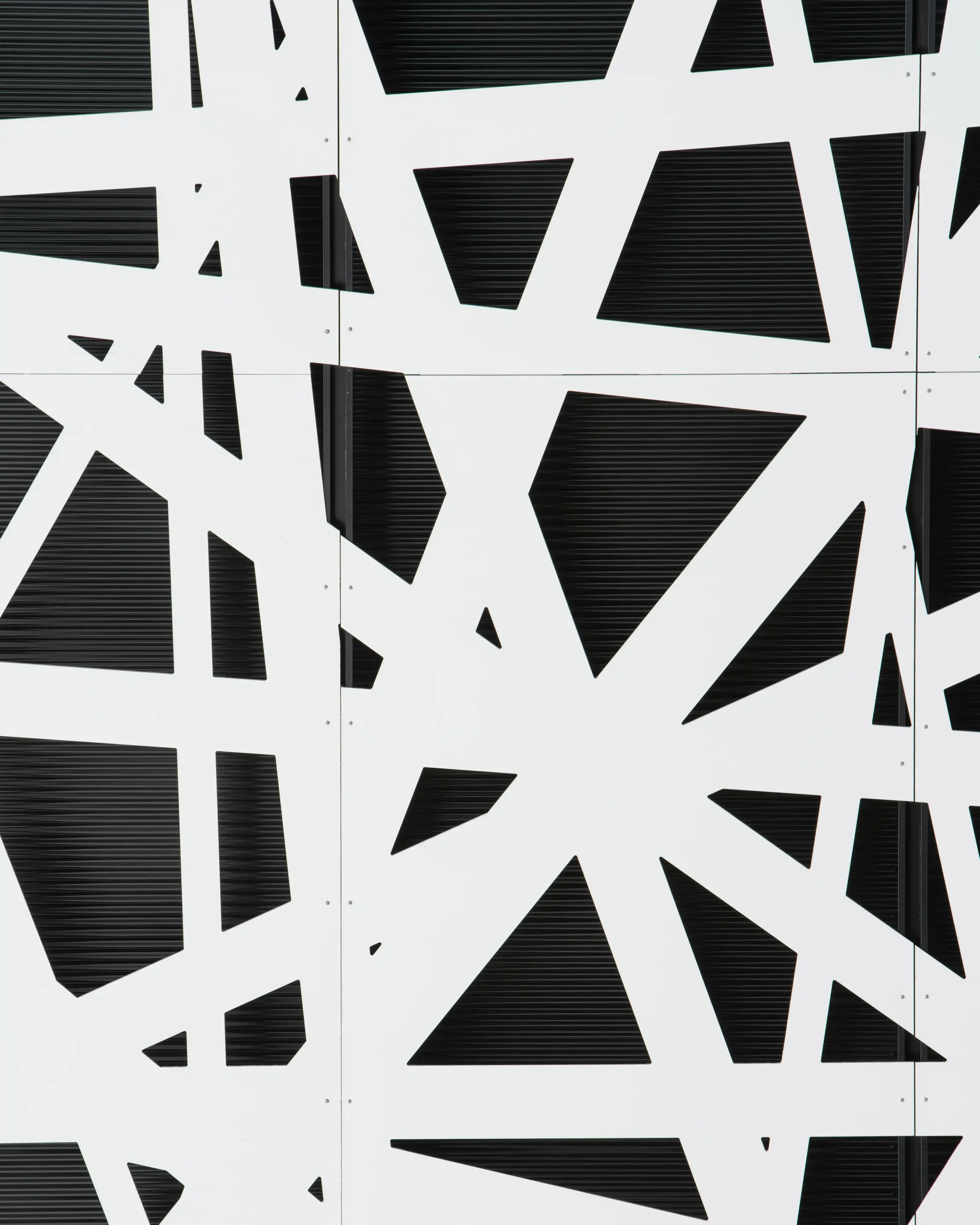
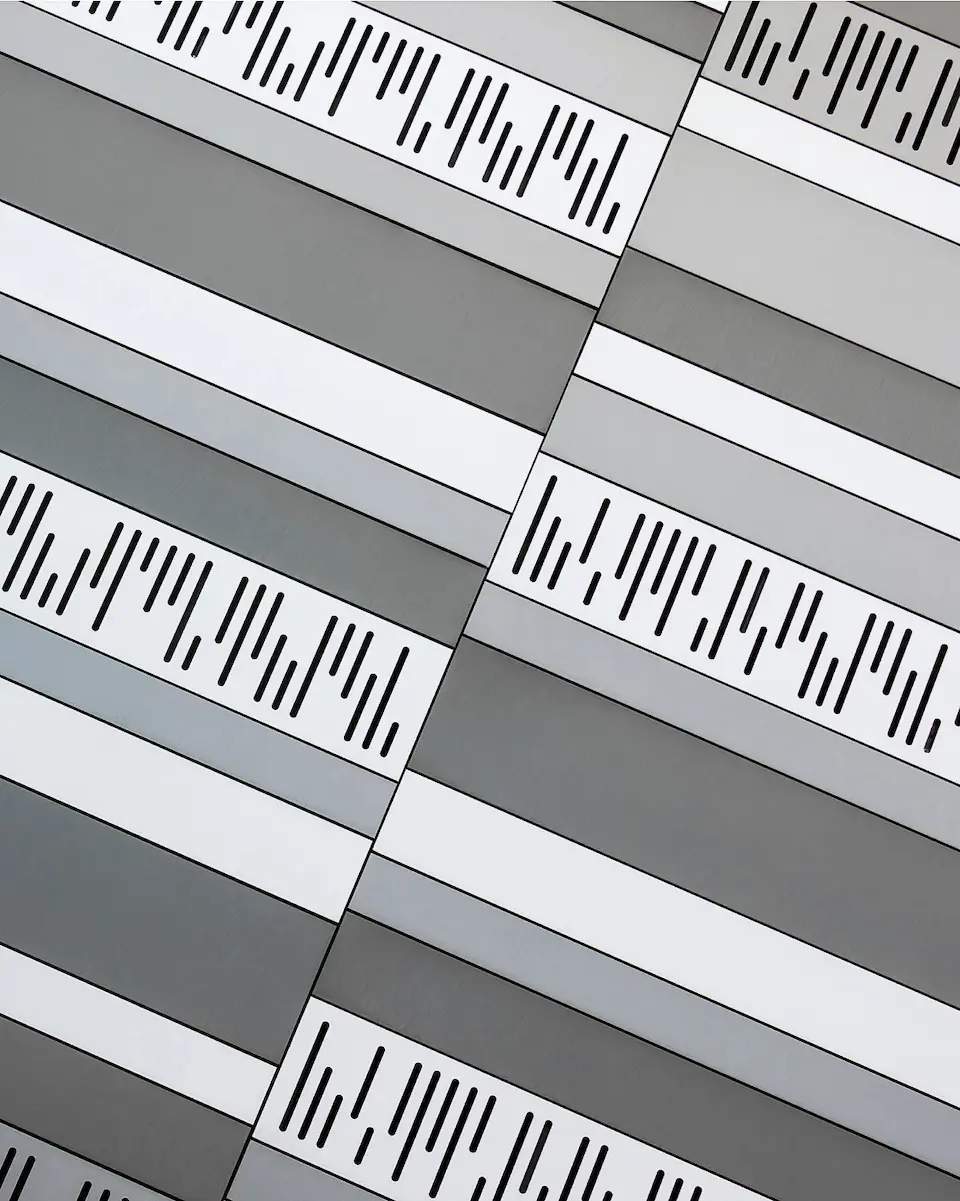
Punching and die cutting
of the composite panel
STACBOND composite panels can be punched and die cut with CNC machinery, adapting the design to the needs of each project, obtaining a clean and precise finish.
We offer all kinds of shapes and varied perforation patterns, as well as the possibility of reproducing complete images such as point clouds, being able to recreate complex designs using different punching patterns.
*Check with STACBOND the recommended parameters to maintain the composite panel properties and the consequent warranty, especially when working with the A2 panel.
Façade coverings with custom designs and functionalities such as ventilation, sun protection or backlighting.
Architectural elements such as railings, hand rails, columns and canopies.
Decorative panels for interiors, such as partition walls, ceiling panels and furniture.
Provide detailed drawings indicating the location, size, and shape of the punching on the plates.
Define the allowable dimensional tolerances for punching, ensuring that project precision requirements are met.
Ensure that punching complies with applicable regulations and standards.
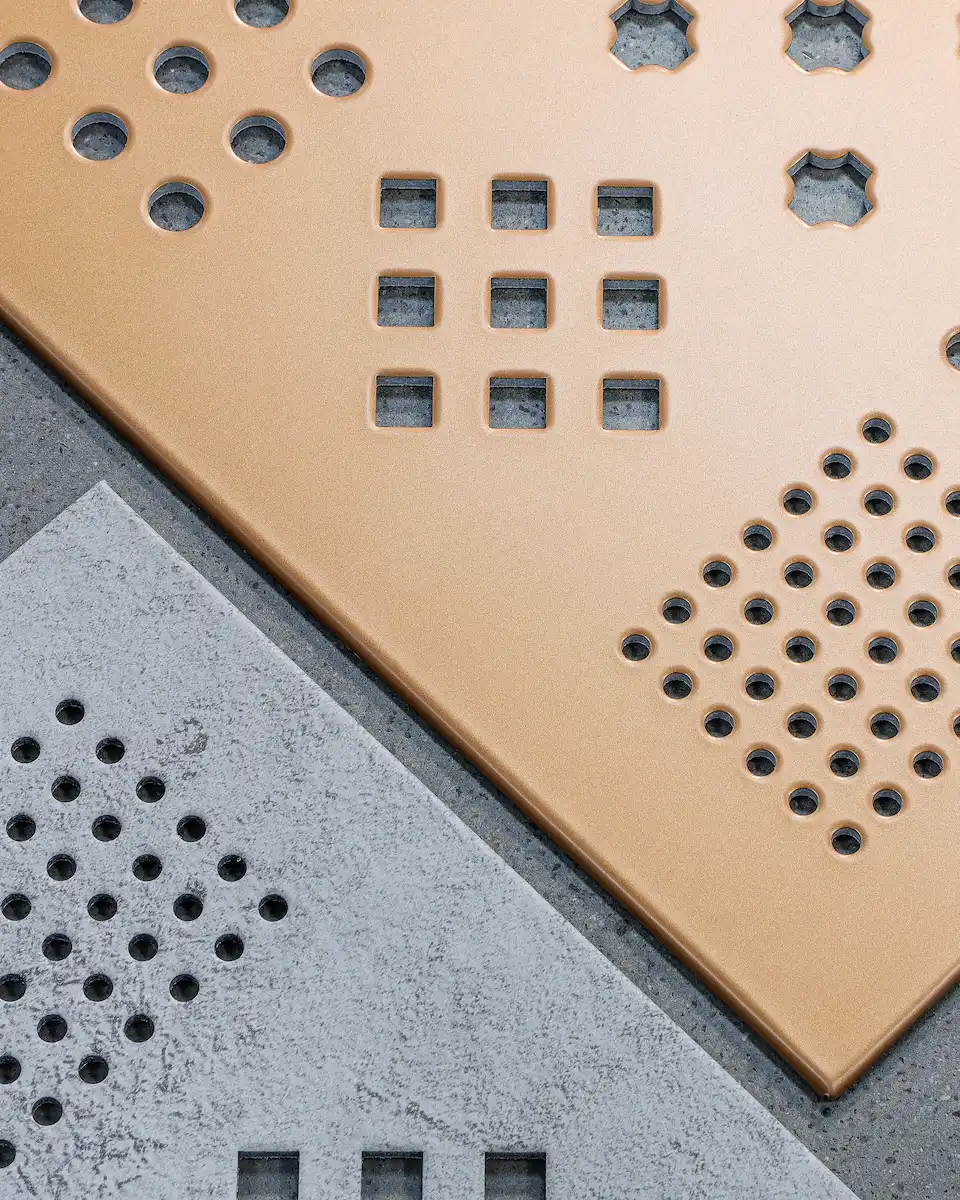
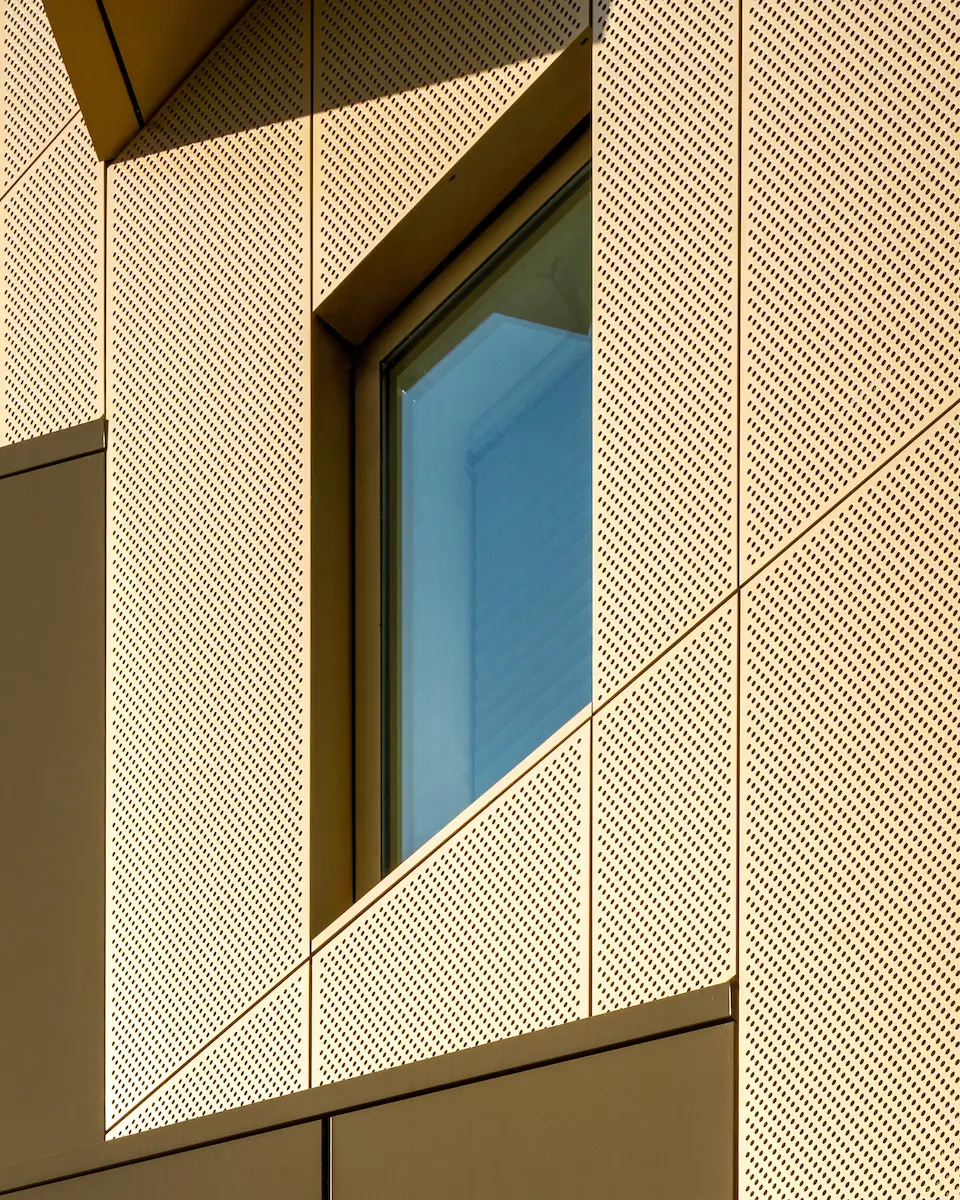
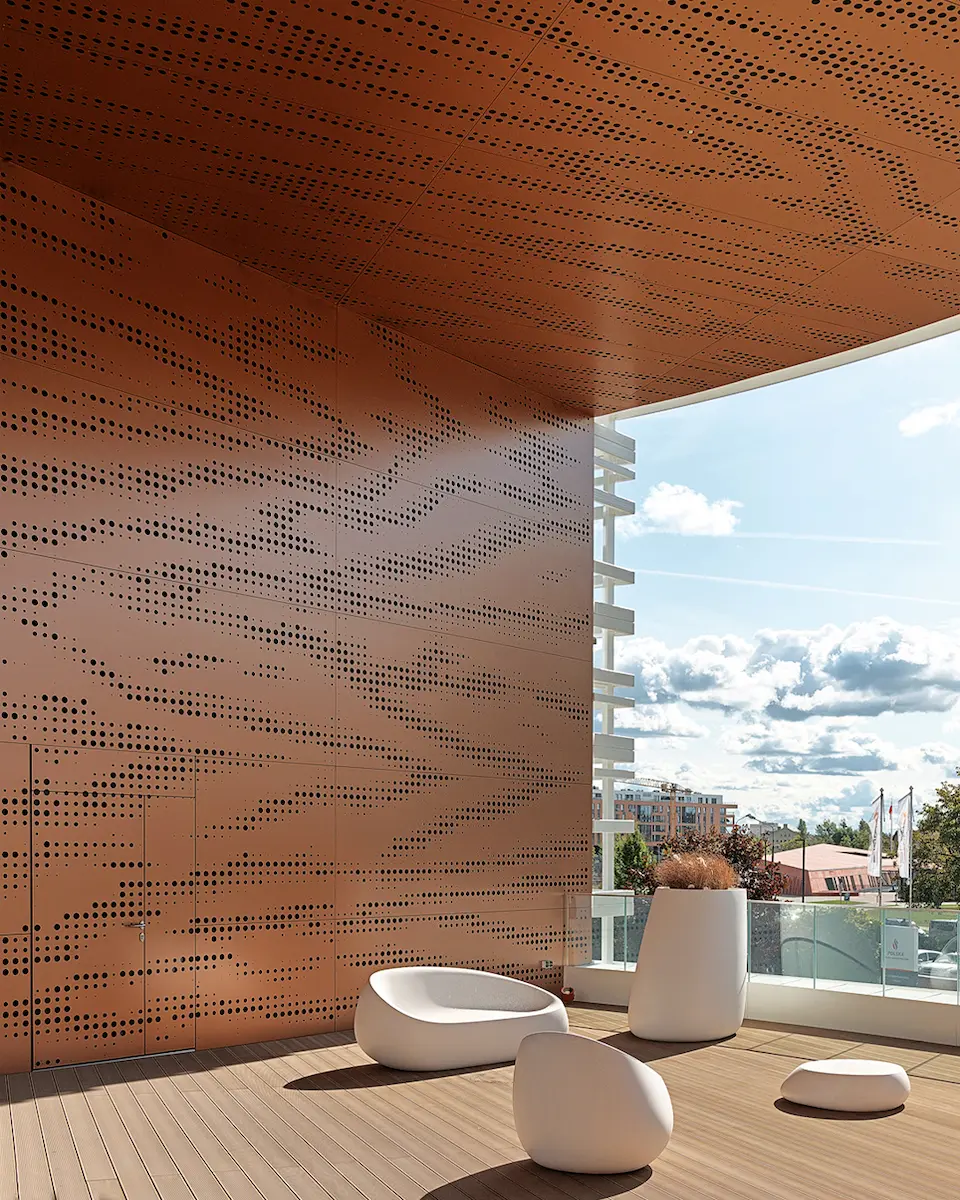
Composite panel stamping
STACBOND composite panels can be stamped using CNC machinery.
This transformation allows you to add relief and depth to the panel, enhancing the visual appearance of the STACBOND composite panel.
A multitude of designs, patterns, sizes and shapes are possible depending on the shape and size of the tools used.
The print allows you to create custom patterns, textures and designs that add a unique aesthetic look to the building’s façade. They are also used in the manufacture of decorative elements for interiors and exteriors. This includes signage, signals, banners, partition walls and patterned ceiling elements that add a touch of style and sophistication to the space.
Define the desired design for the print, considering dimensions and repetitions.
Select the right composite panel, taking into account its thickness, core and finish to ensure that the print meets aesthetic and functional requirements.
Ensure that punching complies with applicable regulations and standards.
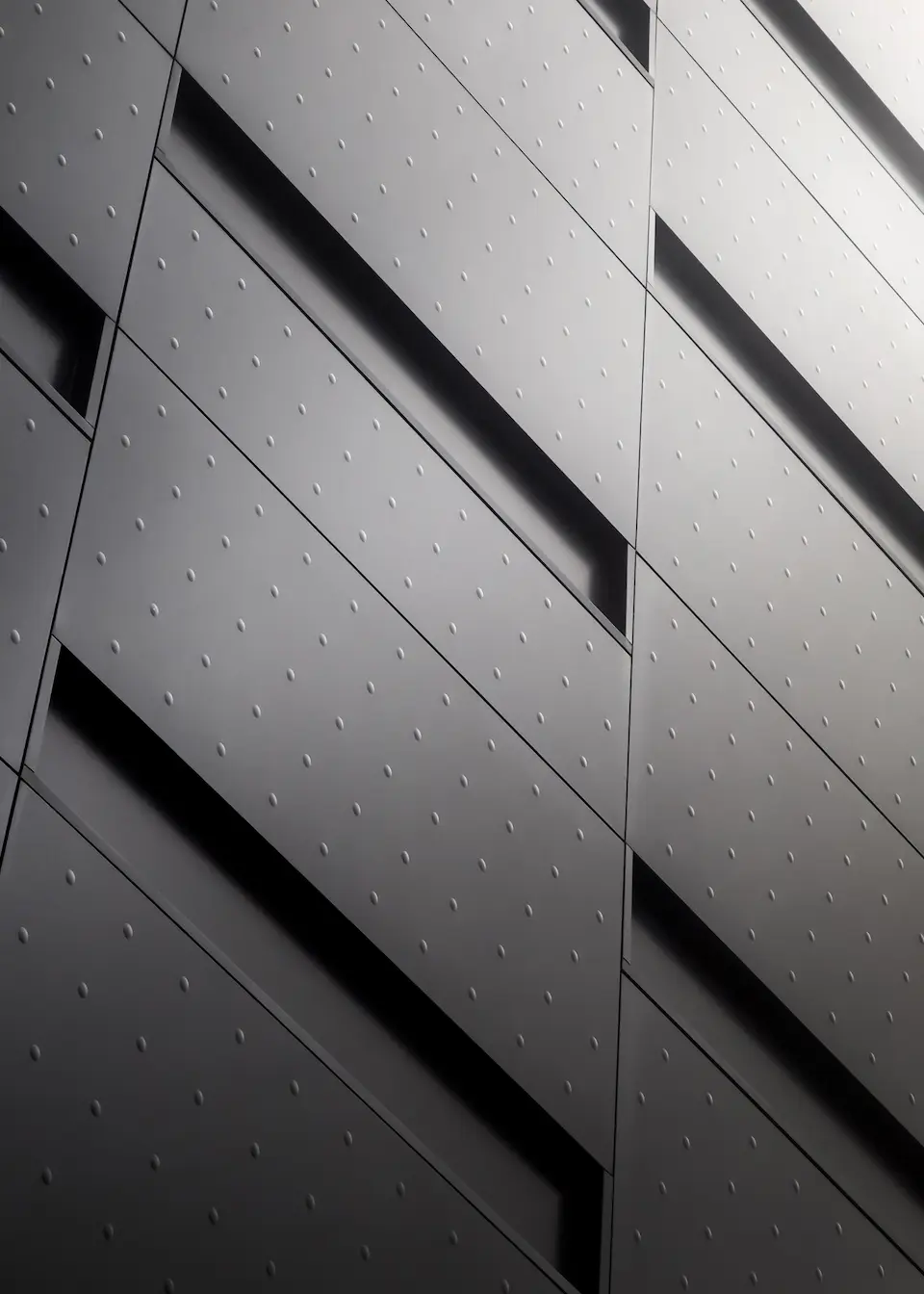
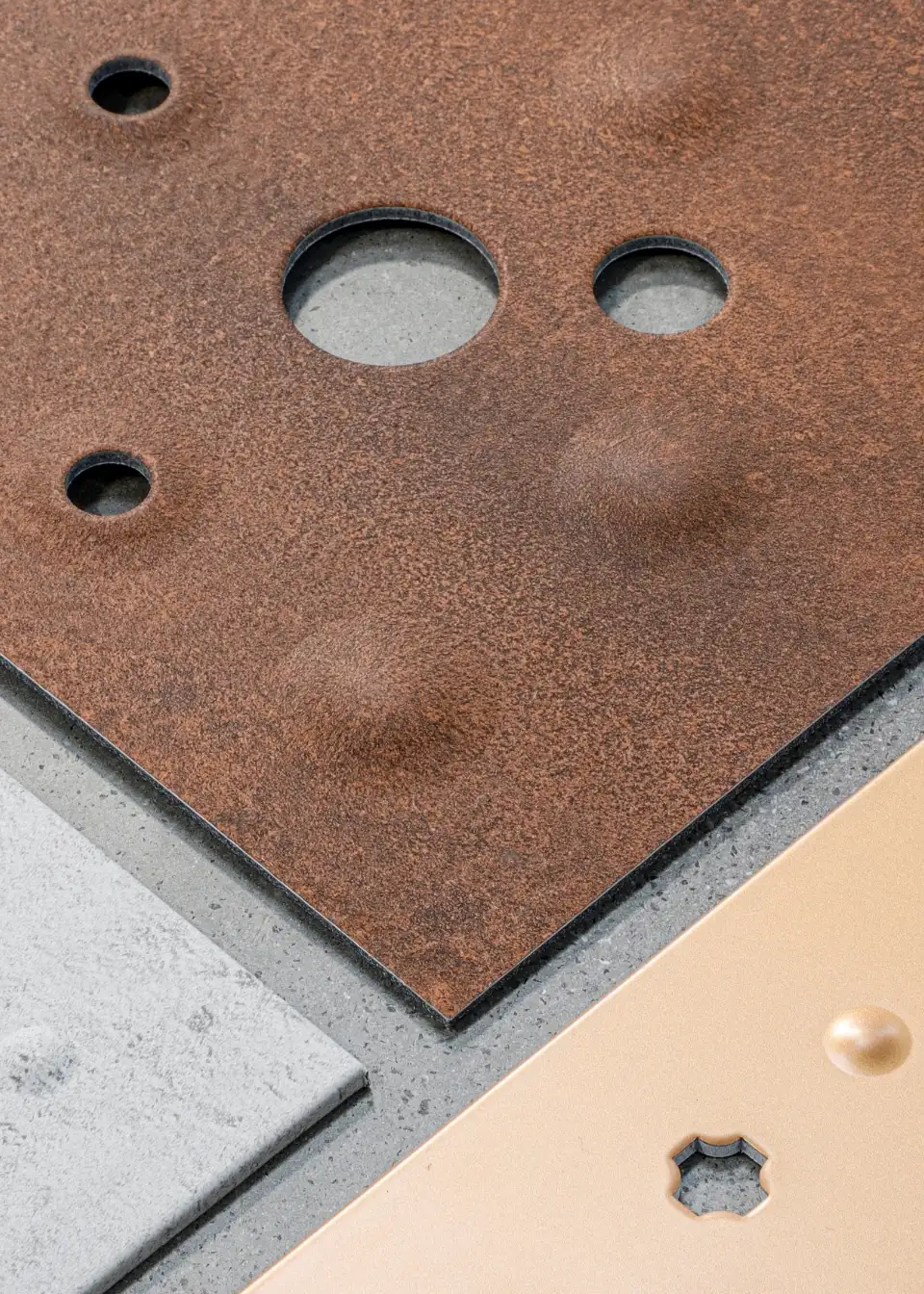
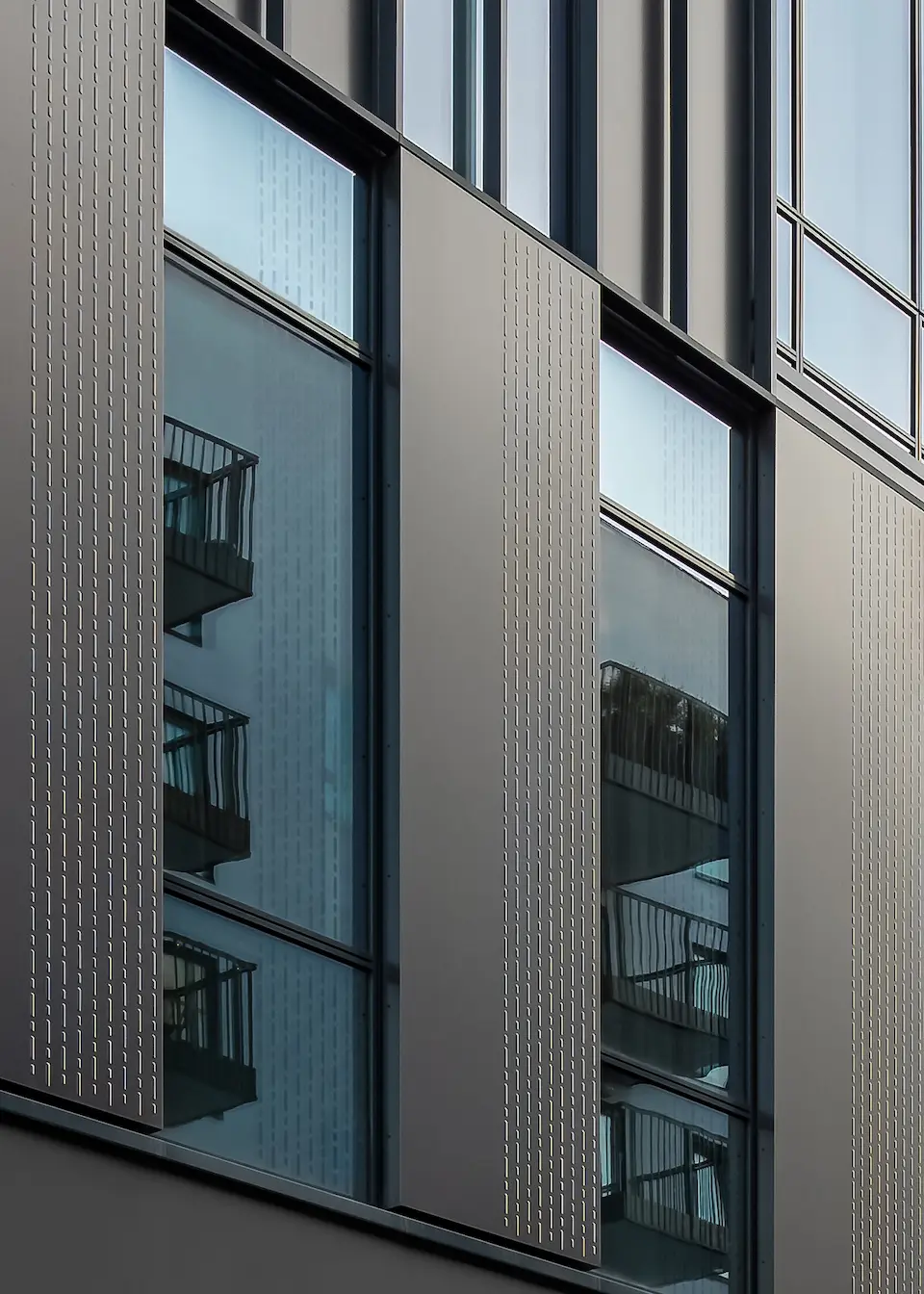
Edging composite panel edges
It is an important technique to improve both the aesthetics and durability of STACBOND panels, edging encloses the panel core, protecting it from the weather and giving the façade a cleaner and more professional appearance.
We can make three types of edges: Single (hides the edge), double interior (hides the edge and part of the rear face) and double exterior (hides the edge and extends a tab that hides the joints with other panel sheets).
In façade cladding this helps prevent premature wear and maintain the structural integrity of the panel over time.
In the creation of decorative elements such as partition walls, ceiling panels and interior coverings, edging the edges ensures a clean finish, with soft and secure edges, contributing to the overall aesthetic of the space.
Provide precise details on desired dimensions, shapes and finishes, as well as specifications on the preferred material type and edging method. Ensure that edges comply with applicable safety regulations and quality standards.
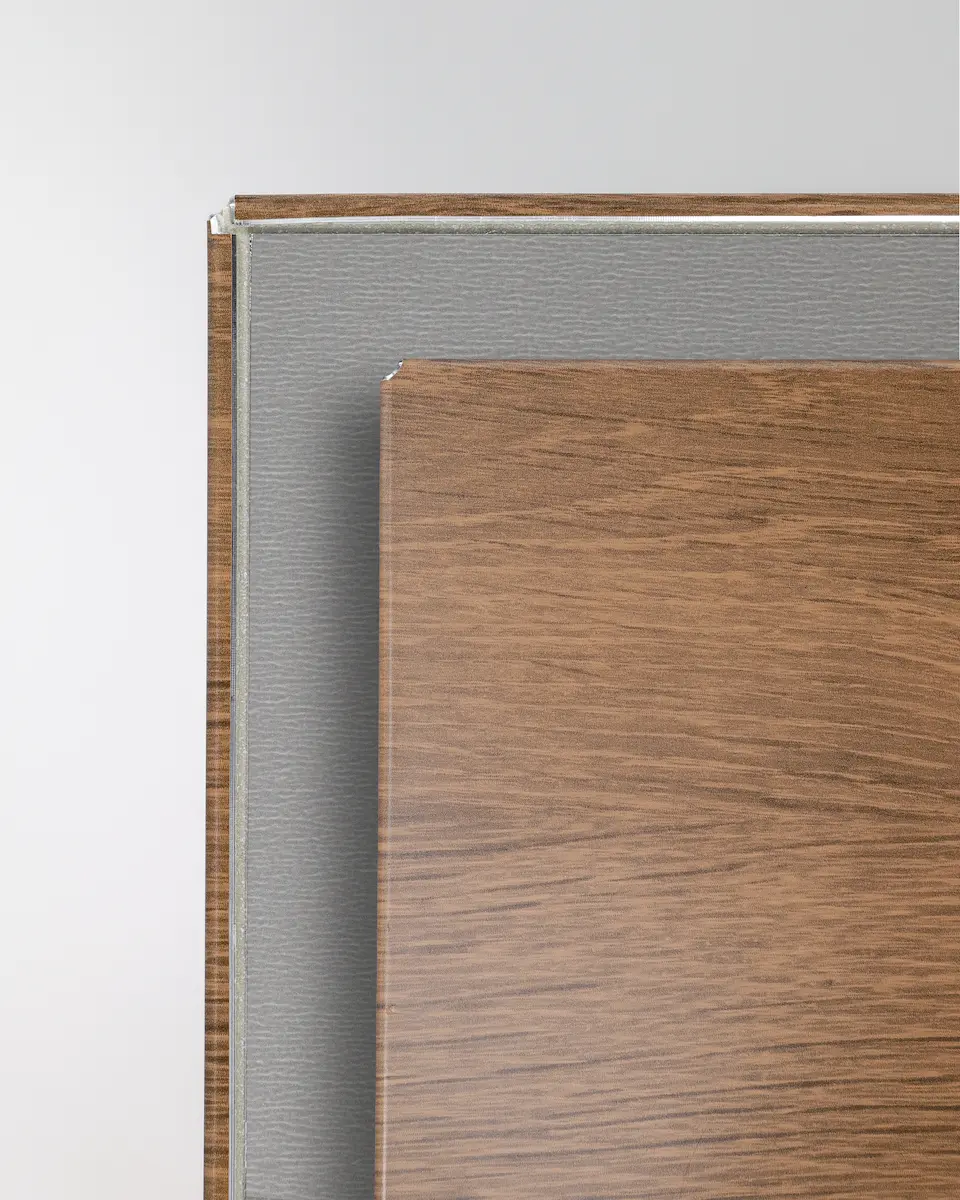
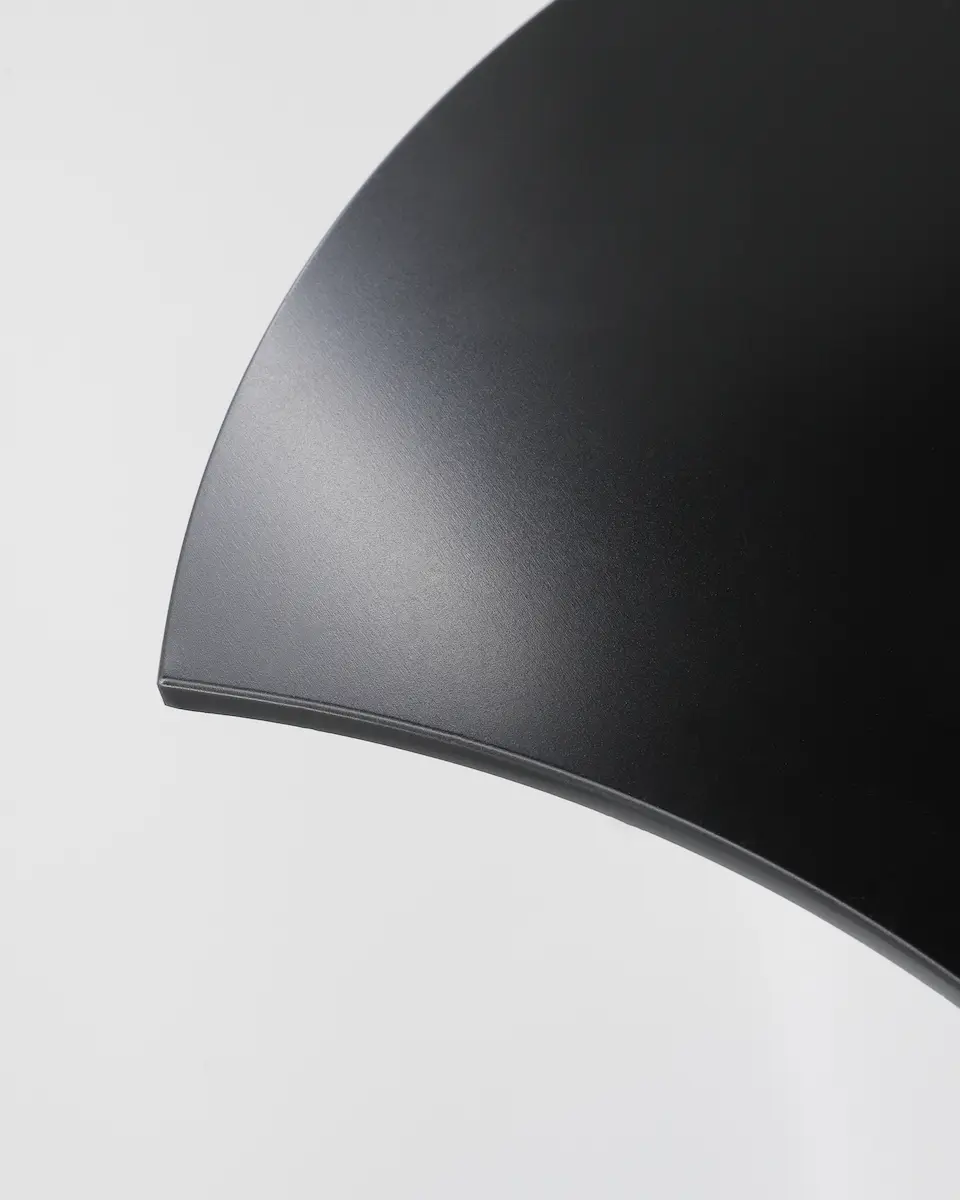
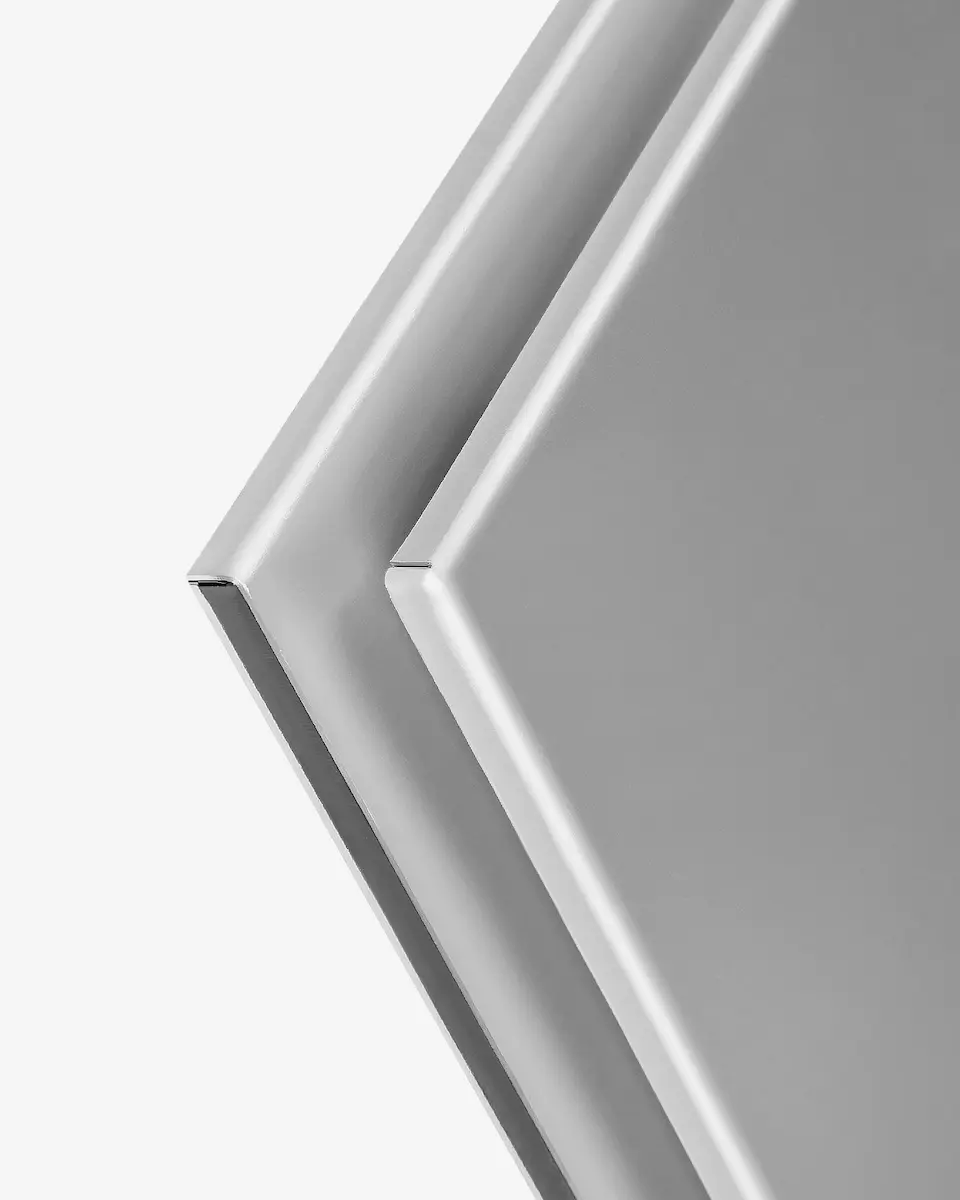
Curving composite panels
STACBOND panels can be curved by roller bending to adapt or smooth-out project surfaces and achieve more organic façade designs.
Bending can be executed in concave and convex directions, vertically or horizontally, in pieces with or without tabs (for visible or hidden installation systems).
In architecture, the curving of STACBOND panels allows the creation of organic and dynamic shapes on the façade, adding visual interest and distinctiveness to the design. The curving of the panels allows columns to be wrapped evenly and elegantly, creating a contemporary and sophisticated appearance. They also provide an aesthetic finish on the corners, edges and finishes of buildings.
It is necessary to have design software that allows three-dimensional models of the panels to be created and simulate the bending process. This helps to optimise the design and ensure curving accuracy.
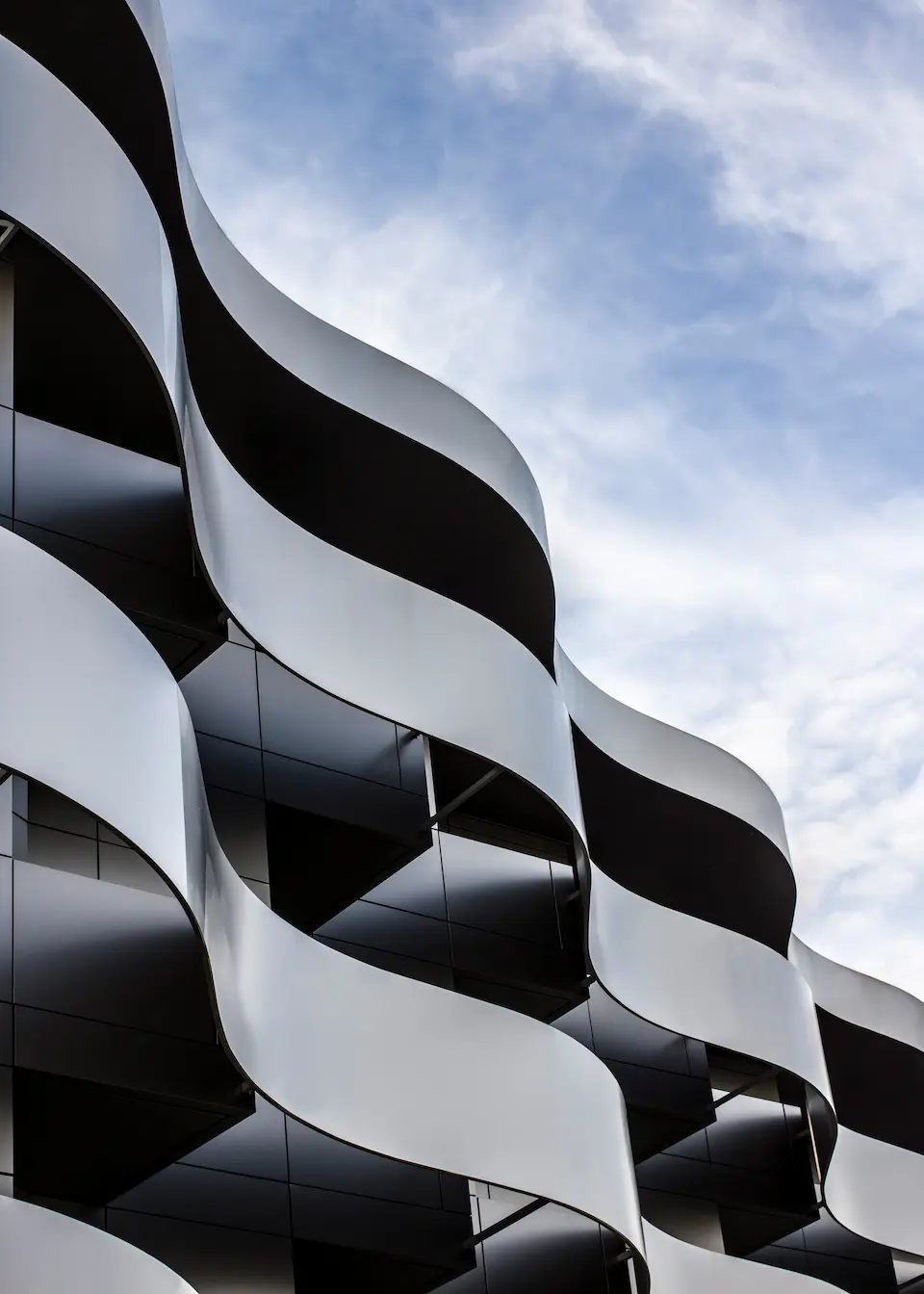
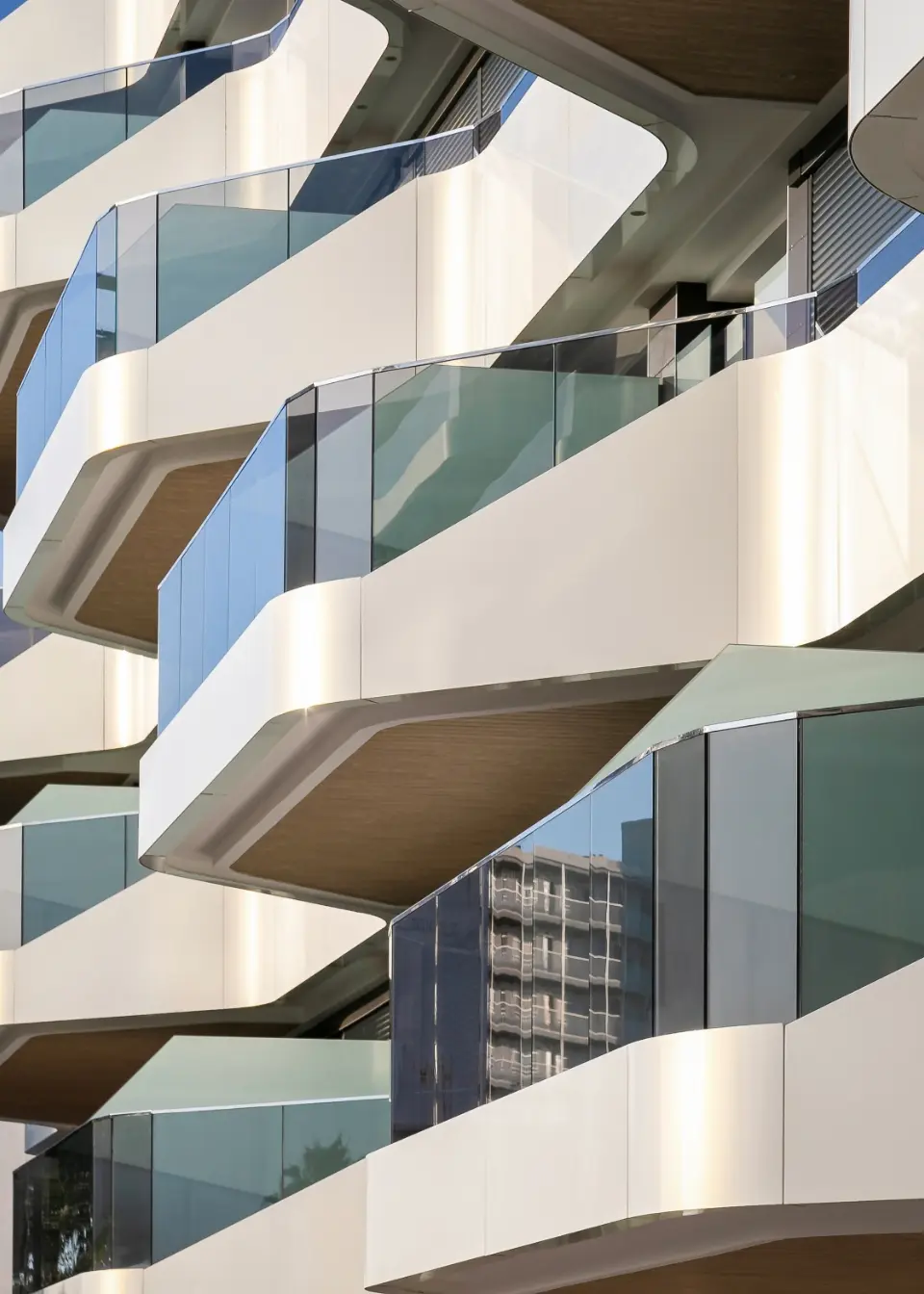
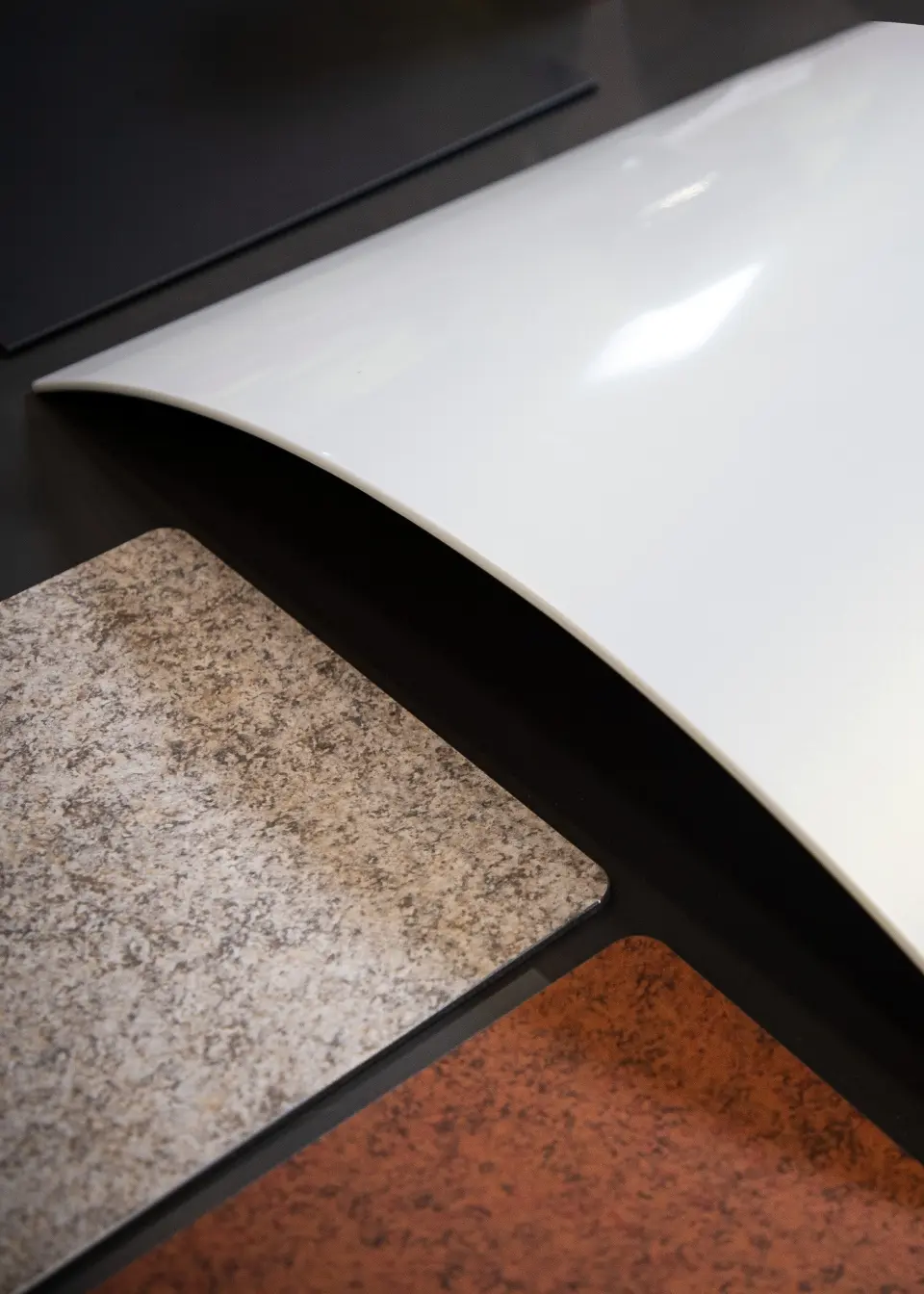
Forming
After machining, the cassettes of the STACBOND systems are formed by folding the edge tabs and attaching them, using specific parts such as plates, rivets or special aluminium profiles.
This process can be executed in the workshop or on site, but always in a clean environment, specially protected and adapted for it.
The shapes of the cassettes are not only limited to the classic rectangular measures of flat appearance, but can also be executed with 3D shapes
One of the most common applications of cassettes is as façade cladding in new buildings and renovations. The cassettes are installed interspersed to create a modern and dynamic appearance, providing protection against the elements and improving the energy efficiency of the building, they also improve interior comfort by reducing the transfer of heat and sound through the façade.
The design of the cassettes must be detailed and precise, including exact dimensions, shapes and specific characteristics of the cassette profile.
STACBOND has developed the software “Sikar panel” that allows optimised machining of the cassettes from the sheet panels, reducing waste.
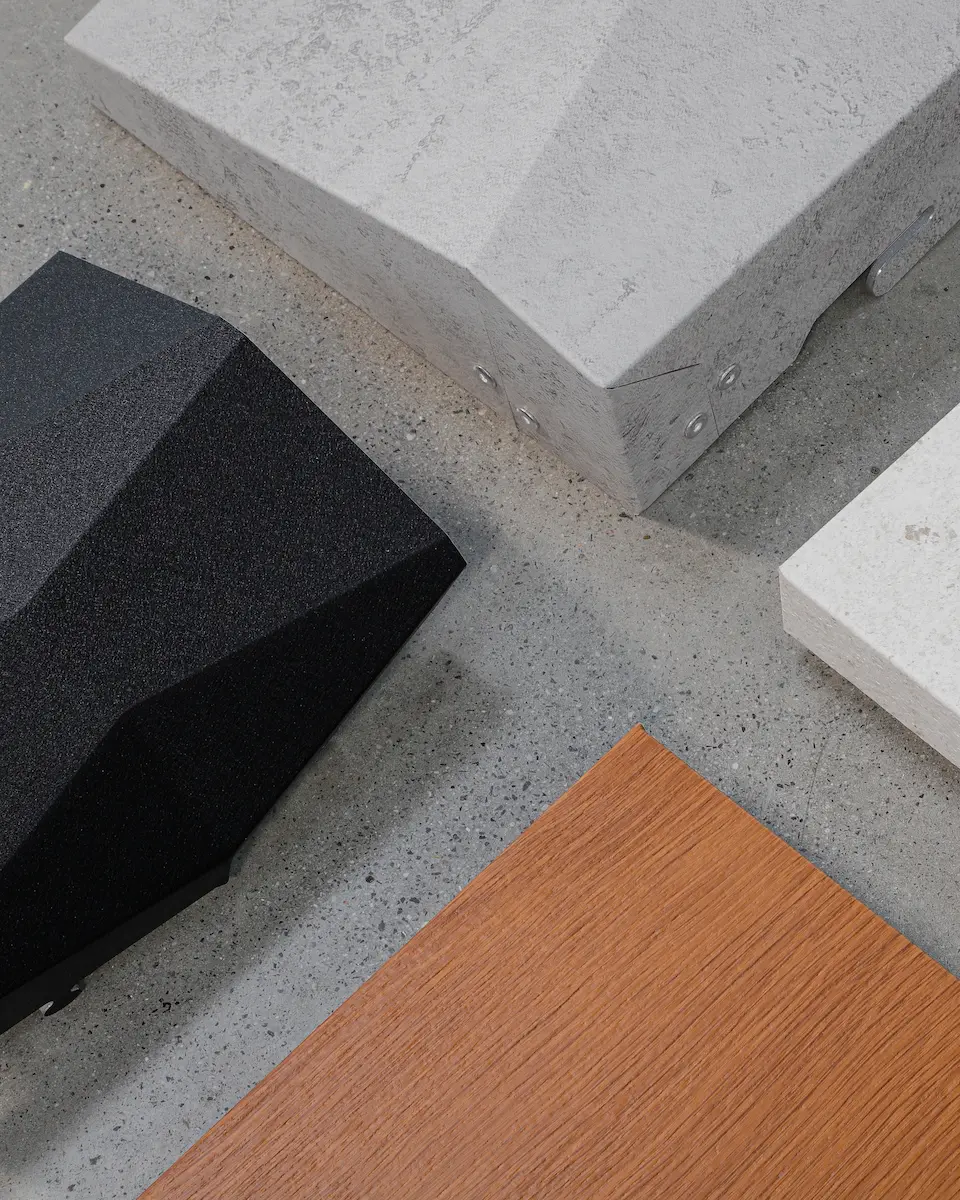
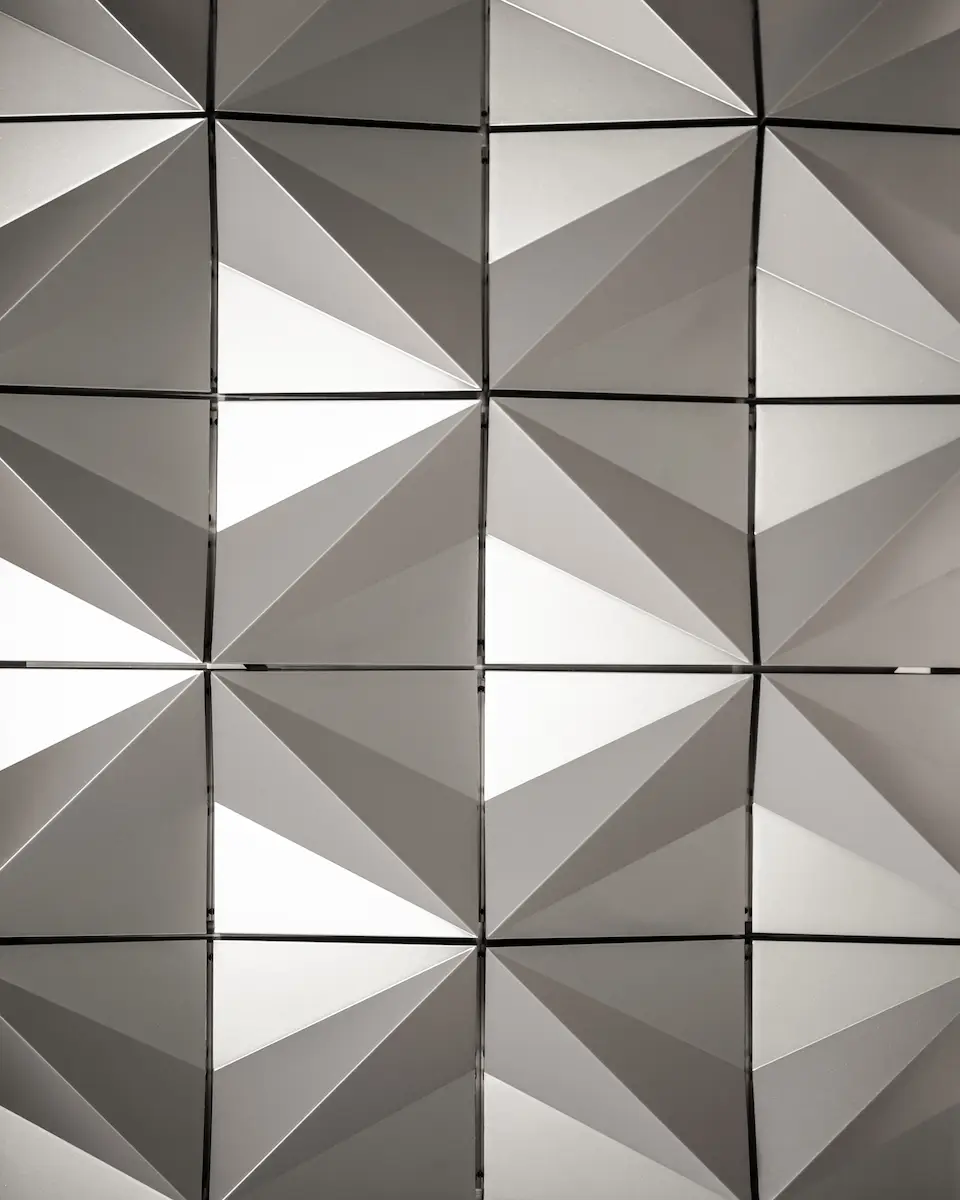
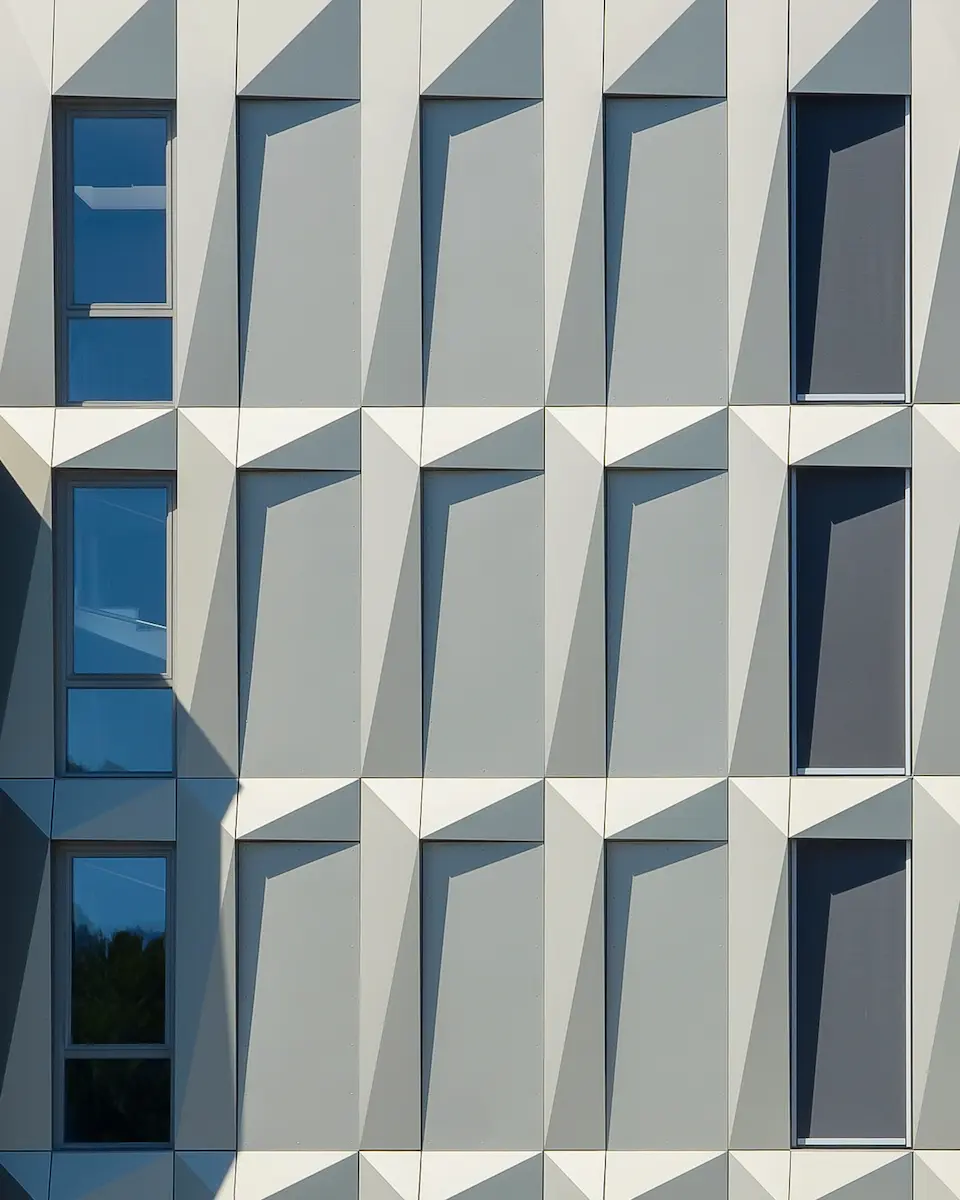
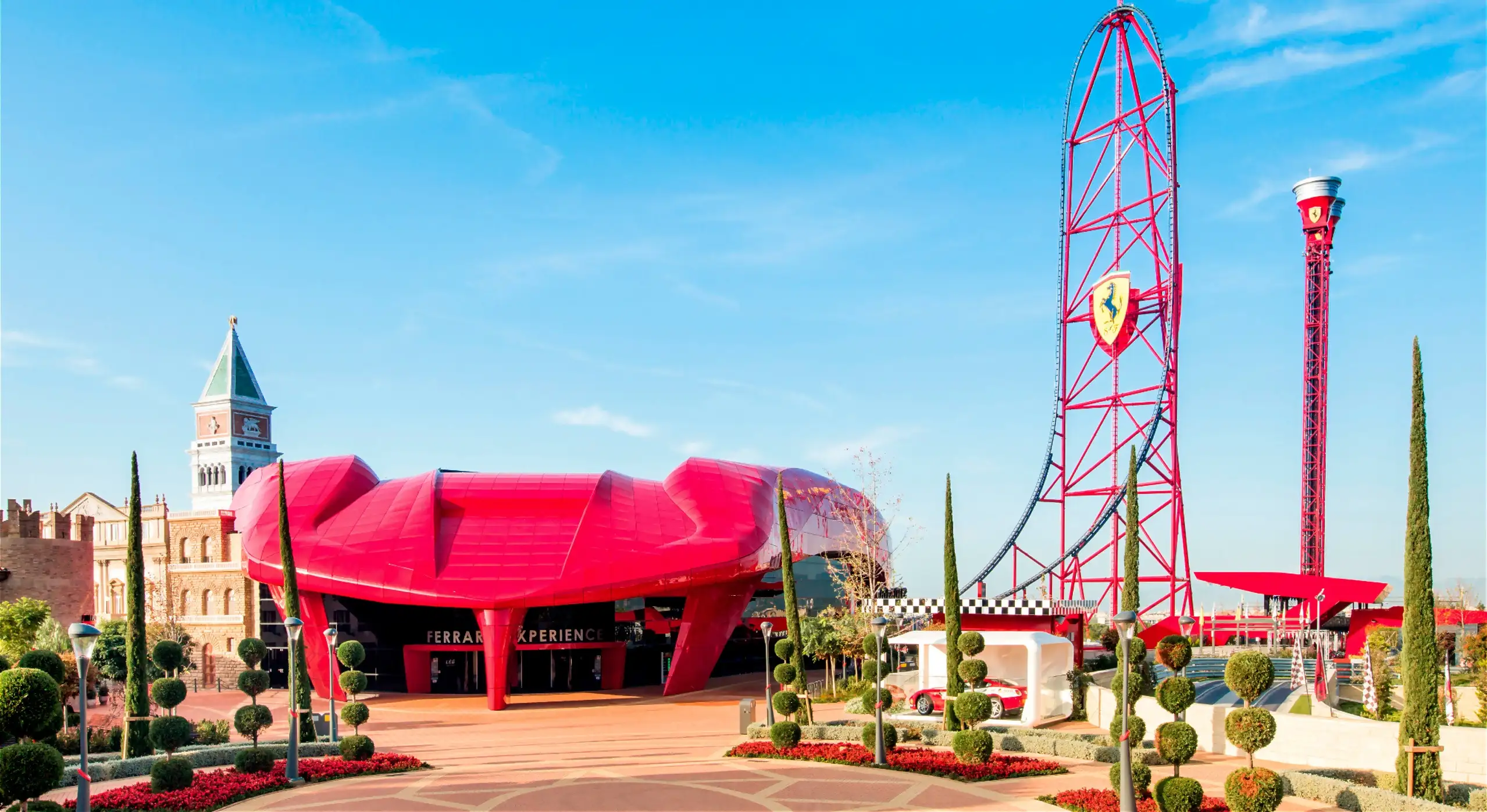
We can make the extraordinary together
As creators and innovators, we understand your search for the daring and unusual. Each façade you design is unique, so each element must adapt perfectly.
STACBOND has collaborated on the development of highñly complex projects such as Ferrari Land at Port Aventura in Salou, Spain, the football stadium of Celta de Vigo, and the exhibition park of Abidjan in the Ivory Coast. If you are working on a unique project and need advice, tell us and we can find the best solution together.